What is an AR (Anti-Reflective) Coating?
An Anti-Reflective (AR) coating, also known as anti-glare coating, is a thin multilayer finish applied to the surface of eyeglass lenses. This coating is designed to reduce the amount of surface glare that reflects off the lenses, thereby enhancing the efficiency of the glasses. AR coatings play a pivotal role in improving visual clarity and comfort, especially in situations where the wearer is subjected to bright lights, such as while using digital screens or driving at night.
The science behind AR coatings involves using layers of material with specific refractive indices that work together to cancel out the light reflections. This not only reduces glare but also significantly minimizes eye strain and fatigue associated with prolonged exposure to bright light sources. Additionally, AR coatings make the lenses nearly invisible, thereby improving the cosmetic appearance of the glasses. They also help in reducing the reflections others see on the lens surface, allowing for better eye contact. With these functional and aesthetic benefits, AR coatings have become a popular choice for enhancing the performance and appearance of eyeglasses.
How Do AR (Anti-reflective) Coatings Work?
The Problem: Surface Reflections
As light passes through a lens from air, it experiences a change in index of refraction. When that occurs, some of the incident light is transmitted through the lens material and refracted while some of the light is reflected. This reflected light is perceived by others as glare and represents a loss of light transmitted through to the eye.
As the refracted light continues through the lens material and reaches the back surface of the lens, there is another index change (lens to air) and again refraction and reflection occur. Reflected light here can bounce off the internal surfaces of the lens and be seen by the wearer as glare, blurred or ghost images. Others may see internal reflections as multiple rings inside the lens (most prevalent in high minus powers). Blurred or ghost images can become intensified at night around bright lights common in dusk or night time driving conditions, and can significantly impair vision. Also, this backside reflection represents further loss of light transmitted through to the eye.
Light coming from the back of the wearer to the back surface of a lens will also undergo a certain amount of reflection. Light here can be reflected directly back to the eye. The results can be a distraction to the wearer or can, in certain conditions, impair vision. For example, bright sun light hitting the back surface of a sun lens that is not AR coated, depending on the angle, can either be reflected directly back into the eye or can "fill" the lens with reflected light. Either case can result in significant vision impairment.
AR coating can minimize front and back lens surface reflections, significantly reducing or eliminating the problems discussed above, reducing eye strain, while allowing more light to reach the eye, improving contrast and clarity.
The Solution: Fight Reflections with Reflections
AR coatings reduce lens surface reflections through a process called destructive interference, by actually generating reflections of its own. The index of refraction of the AR layer is in between that of the lens medium and that of air. Light incident upon an AR coated lens experiences reflection at both the AR layer and the surface of the lens. However, the thickness of the AR layer is such that the light waves reflected from the AR surface are 180° out of phase with light waves reflected from the surface of the lens. Consequently, the reflected light waves undergo destructive interference and effectively cancel each other.
Fun Fact: The Law of Conservation of Energy states that energy can neither be created nor destroyed. So, what happens to the energy from the cancelled light waves? It is transferred through the lens medium to the patient's eyes improving contrast and clarity!
In Depth: An Interview with Norm Kester, founder of Quantum Innovations on the Process of AR Coating
Premium AR Coating Upgrades
Hydrophobic and oleophobic coatings are significant enhancements often applied in conjunction with Anti-Reflective (AR) coatings on eyeglass lenses. These coatings play a vital role in maintaining the clarity and longevity of the lenses, further enhancing the wearer's visual experience.
What is a Hydrophobic Coating?
Hydrophobic coatings, as the name suggests, repel water. This means that when water comes into contact with a lens equipped with a hydrophobic coating, it beads up and rolls off rather than spreading and smearing. This characteristic is particularly beneficial in rainy conditions or during activities that involve water, such as boating or fishing. It ensures that the wearer's vision remains unobstructed by water droplets. Additionally, the hydrophobic properties help to prevent fogging, a common issue in humid environments or when moving between different temperatures.
What is an Oleophobic Coating?
Oleophobic coatings, on the other hand, are designed to repel oils. This includes the natural oils from a person's skin, which can be transferred to the lenses during handling. By repelling these oils, oleophobic coatings help to keep lenses free from smudges and fingerprints. This property is especially valuable for individuals who frequently need to adjust or touch their glasses. The reduced adherence of oils and other substances also makes the lenses easier to clean and maintain, contributing to better lens hygiene.
When combined with AR coatings, hydrophobic and oleophobic coatings contribute to a superior lens performance. AR coatings alone significantly reduce reflections and improve visual clarity, but they can sometimes be prone to smudges and moisture. The addition of hydrophobic and oleophobic properties ensures that the AR coating can function optimally by keeping the lens surface clear and clean. This combination results in a lens that not only provides sharp, clear vision through reduced glare but also remains cleaner and clearer during everyday use, enhancing the overall satisfaction and experience of the eyewear.
More Information: Keep Lenses From Slipping Edging Super-Hydrophobic Coatings
Benefits of Anti-Reflective Coating
- Improves the appearance of your glasses (and your eyes). Anti-reflective coatings make lenses appear nearly invisible without surface reflections, so people your eyes. This becomes even more apparent on camera; in photos, videos, and video calls, particularly if you have light directly in front of you reflecting off of the lenses.
-
Improves Visual Clarity: With an anti-reflective coating, a greater amount of ambient light can reach your eyes, unobstructed by lens reflections. This optimized light transmission results in clearer, more acute vision, allowing you to perceive your surroundings with enhanced sharpness and detail.
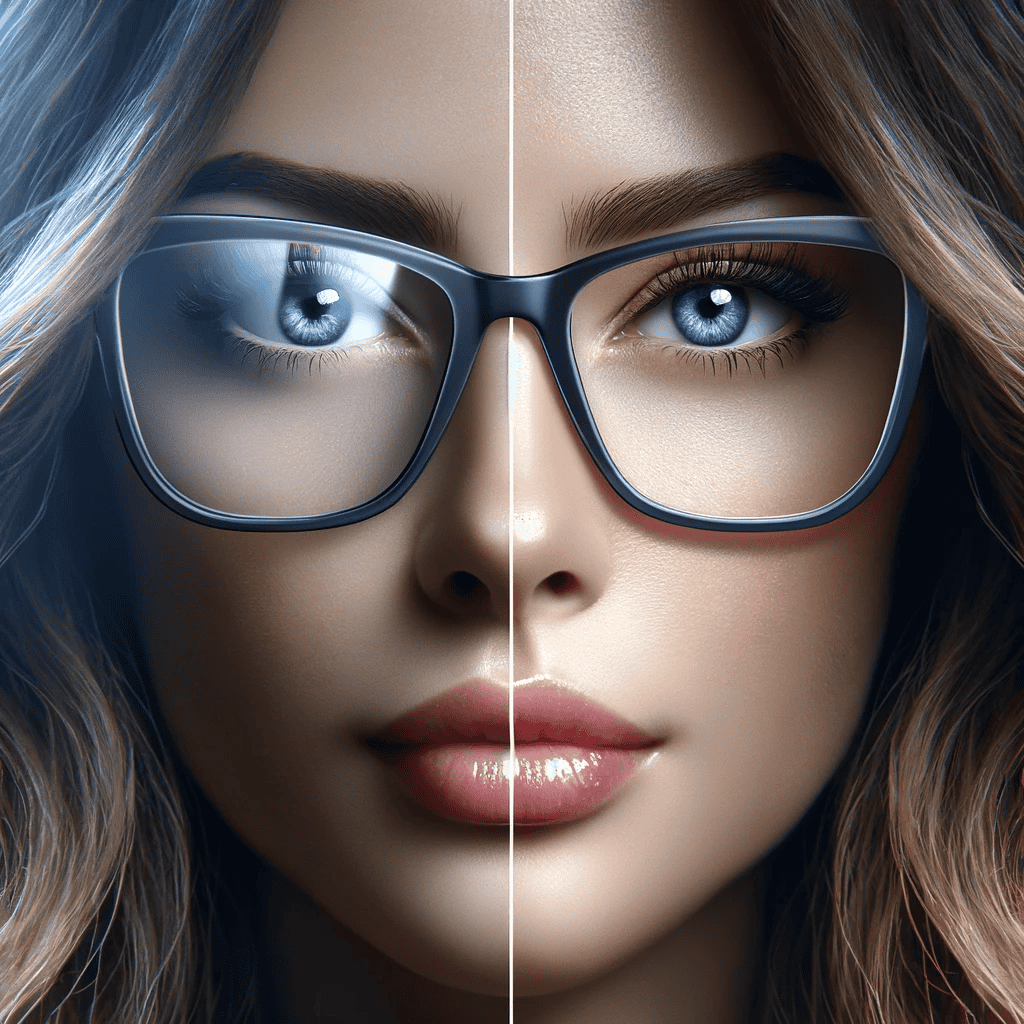
- Minimizes Eye Fatigue: The reduction of reflections on your lenses facilitates more comfortable viewing of fine details and text, thus alleviating eye strain. The anti-reflective coating is particularly beneficial for those frequently using computers, as it mitigates the glare from screens, and for night drivers, as it reduces the halo effect from streetlights and oncoming headlights.
Anti-reflective coating becomes even more important when you have a stronger prescription that calls for high-index lenses, which tend to reflect more light than other types of eyeglass lenses.
How Are Anti-Reflective Coatings Applied?
The application of AR coatings is a complex, high-tech process that requires precision and cleanliness. The process is typically conducted in a vacuum chamber to ensure the purity and adherence of the coatings. Here’s a step-by-step overview:
- Cleaning: The lenses are thoroughly cleaned to remove any dust, oils, or other contaminants. This step is crucial because any residue on the lenses can interfere with the uniformity of the coating.
- Preparation: After cleaning, the lenses are placed in a special rack or holder designed to keep them stable and properly oriented during the coating process. The environment is controlled for temperature and humidity to ensure optimal conditions.
- Applying the Hard Coat: Before the AR coating, a hard coat layer is typically applied. This involves dipping the lenses into a solution containing the hard coat material, followed by thermal curing. Heat treatment activates the hard coat, creating a tough, protective layer, improving the scratch resistance of the lens material.
- Preparation: Again the lenses are cleaned and prepared to accept the deposition of the AR coating.
- Deposition: The AR coating is applied through a process called vacuum deposition. In this step, the coating material is vaporized in a vacuum chamber and then condenses on the surface of the lenses. The process allows for the layers of the coating to be built up one at a time, with precise control over the thickness and composition of each layer.
- Layering: AR coatings consist of several layers of metal oxides of varying refractive indices. These layers are carefully designed to interfere with the reflected light waves, reducing reflection through destructive interference. The precise number of layers and their composition depends on the specific requirements of the lens and the desired characteristics of the AR coating.
- Curing: After the layers have been applied, the coated lenses are subjected to a curing process, which can involve heat or UV light. This step solidifies the coating, ensuring its durability and adherence to the lens surface.
- Quality Control: Once the lenses are coated and cured, they undergo a thorough inspection for any defects or irregularities. Only lenses that meet stringent quality standards proceed to the final packaging and distribution.
Anti-Reflective and Hard Coatings
AR coating is a thin, multilayered application on eyeglass lenses designed to reduce reflections, allowing more light to pass through. This improves vision clarity and reduces glare from digital screens and headlights. A thermal cured hard coat, on the other hand, is applied to make lenses more resistant to scratches and impacts, extending their usable life.